Floor Shield Commonly Asked Questions
Your home is one of your most valuable assets; safeguarding it with fresh paint or a new coating system is crucial. However, homeowners frequently ask, “How much does it cost to coat my floor?” and “What exactly am I paying for?” At Floor Shield, we’re here to provide the answers you need to be confident in your potential investment.
We want to be transparent in the evaluation of our prices compared to the competition, though. At the end of the day, it’s better for both us and you to know everything that separates Floor Shield from other brands, even if we must tackle our downsides.
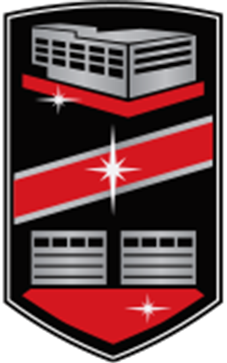
HOW EXPENSIVE IS FLOOR SHIELD COMPARED TO OTHER OPTIONS?
Before we compare costs, you should understand your coating options. Epoxies are the tried-and-true coating system and have been around for many decades. There are many good things about epoxies:
- Great adhesion
- Lower cost
- Many applications
At Floor Shield, we manufacture epoxies, but when it comes to your garage, patio, basement, or pool deck, there are much better options.
Usually, epoxies are typically a multi-day installation. They are not UV stable (meaning they yellow) and they typically have a strong, long-lasting odor.
Yellowing Garage Floor Apron: Source Floor Shield Dealer Network
Your next best option is a Polyurea coating system. Most polyurea are “blended systems,” meaning your installer will use a polyurea base coat and a polyaspartic top or clear coat. The advantages of this are:
- You can install most residential applications in one day.
- They are mid-range in price.
- Low odor.
Like epoxies, polyureas are not UV-stable, and based on independent lab tests, they have 40% less adhesion than Floor Shield Polyaspartic. Adhesion is the most important aspect of any coating.
Polyaspartics are the best technology and fastest-growing segment of the concrete coatings industry. Floor Shield Polyaspartics can be installed in just a few hours, are UV stable, and have zero VOC’s (Volatile Organic Compounds).
Let’s talk about the cost.
- Floor Shield’s average cost is between $6 to $9 per square foot.
- The average cost of a traditional epoxy coating is between $3 to $10 per square foot.
- The average cost of a polyurea is between $6 to $8 per square foot.
We are happy to provide a free quote to get an exact price for your unique concrete coating project. We simply need to assess your concrete, measure and review options with you.
FACTORS THAT INFLUENCE PRICE
There are many variables that go into the total cost of coating your concrete floor. The variations in cost depend on factors such as:
- Condition of the floor
- Labor costs
- Square footage of the floor
- If extensive surface repair or leveling is needed
The main reason for Floor Shield's price range lies in its resilience and convenience.
- UV stability
- Anti-slip
- Unmatched abrasion resistance
- Superior adhesion
- Same-day floors
- Ease of installation
- Low VOCs (Volatile Organic Compounds)
- Excellent stain resistance (including hot tire pickup)
- Variety in color and flake options
It should be noted that although the initial investment in Floor Shield is higher than most epoxies and polyureas, you’ll save more in the long term, especially if your concrete floor has any parts exposed to the sun. Unlike epoxies and polyureas, which amber and fade when exposed to UV rays, Floor Shield retains its color and gloss.
Going the DIY route will save you money, but you’re sure to encounter problems with the application when a professional is not present. You’ll also lose out on an industrial-grade product.
THE INSTALLATION PROCESS OF FLOOR SHIELD
The installation of Floor Shield has a thorough process of steps to ensure your investment is secure.
-
Floor Testing:
- Conduct thorough testing of the floor, including hardness and moisture level assessment.
- Perform a Mohs test to measure concrete hardness through scratching. This provides pad recommendations for optimal grinding.
- Utilize a moisture meter to determine the moisture content of the concrete pad.
-
Surface Protection:
- Safeguard surrounding areas, such as driveways and side walls, to prevent product spillage.
- Use materials like Ram Board or equivalent to protect non-targeted surfaces.
-
Crack Patching:
- Identify and patch all cracks in the concrete to ensure a smooth surface.
-
Concrete Grinding:
- Grind the concrete surface to achieve an even level.
- Grinding gives a better edge for the product to adhere to.
- Note: Some companies may opt for acid etching to save time and cost, but it may result in uneven surfaces.
-
Dust Removal:
- Ensure the removal of any silica or dust particles from the floor to prepare it for the next steps. This is vital to create proper adhesion.
-
Moisture and Softness Mitigation:
- Address issues with soft concrete by taking necessary steps to harden it.
- Apply a moisture-vapor barrier coating if excessive moisture is present to prevent coating failure.
-
Color Coat Application:
- Apply the color coat to the prepared concrete surface.
-
Flake Application:
- Broadcast flakes over the color coat for an aesthetic look and extra protection.
-
Clear Coat Finish:
- Apply a clear coat to protect the flakes and enhance the floor's appearance with a glossy finish.
-
Clean-Up:
- Thoroughly clean the work area to leave it in better condition than when the project started.
- This comprehensive installation process ensures that your concrete floor is properly prepared, coated, and protected, resulting in a high-quality finished product.